The efficiency of a 10 t/h animal feed manufacturing machine is essential for producers looking to satisfy the increasing demand for high-quality animal feed. Numerous factors can significantly impact the production efficiency of these machines, influencing output, quality, and operational costs. Understanding these factors is vital for optimizing performance and ensuring profitability. This article examines the key factors that affect the production efficiency of a 10 t/h animal feed manufacturing machine.
1. Quality of Raw Materials
The quality of the raw materials used in feed production is one of the most crucial factors affecting efficiency.
- Moisture Content: The moisture content in raw materials is critical for the conditioning and pelleting processes. Ideal moisture levels (generally between 12-16%) promote better gelatinization of starches, leading to improved pellet formation. Excessive moisture can cause clumping and hinder flowability, while insufficient moisture can result in poor pelleting.
- Particle Size: The particle size of raw materials impacts the surface area available for conditioning and pelleting. Finer particles enhance mixing and conditioning, which improves pellet quality. However, overly fine particles can increase friction and energy consumption during pelleting, reducing overall efficiency. Thus, achieving an optimal balance in particle size is essential.
- Ingredient Composition: The nutritional makeup of raw materials also affects production efficiency. Ingredients with higher starch content tend to gelatinize better during conditioning, enhancing pellet quality. Conversely, high crude fiber content may necessitate the addition of fats to reduce friction during pelleting, impacting overall efficiency.
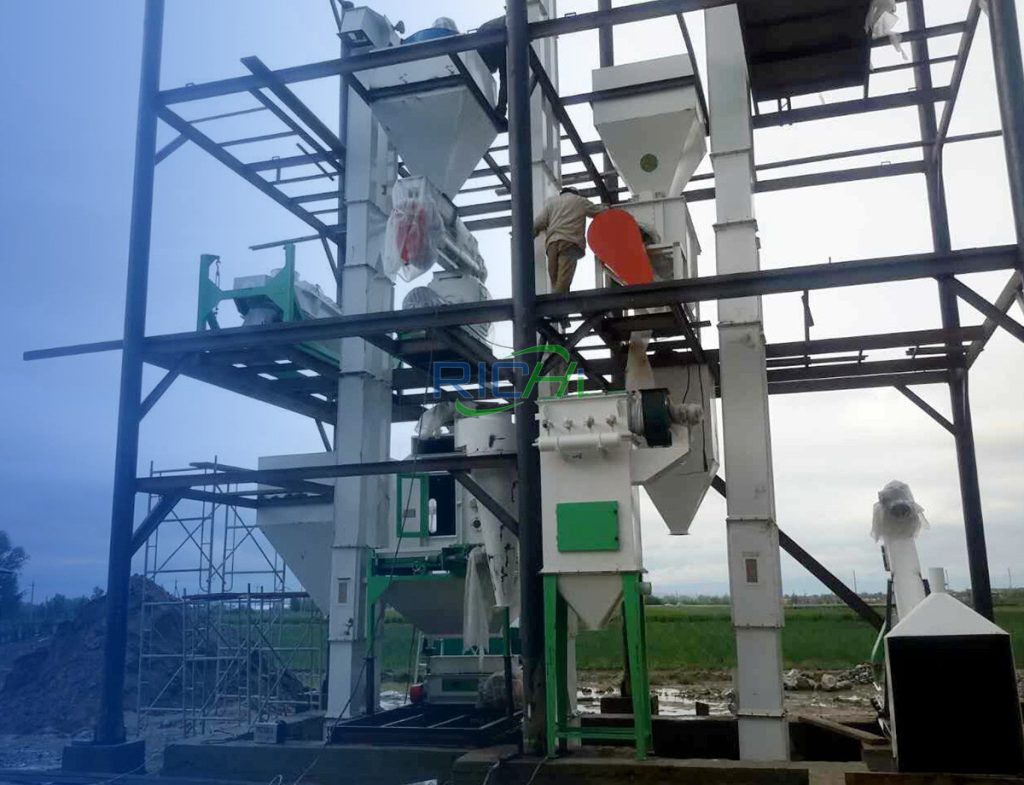
2. Machine Design and Technology
The design and technology of the animal feed making machine are crucial in determining production efficiency.
- Pelleting Technology: The type of pelleting technology employed, such as ring die or flat die, influences the efficiency of the pelleting process. Ring die pellet mills are typically more efficient for larger production volumes, yielding better pellet quality while reducing energy consumption.
- Conditioning Systems: Advanced conditioning systems that include steam and moisture control can improve the gelatinization of raw materials, enhancing pellet quality and production efficiency. Proper conditioning ensures that materials are well-prepared for pelleting, which reduces wear on the machine and increases output.
- Automation Features: Machines equipped with automation capabilities can optimize production processes by adjusting parameters in real-time. This allows for better control over feed flow rates, temperature, and pressure, ensuring consistent production and minimizing waste.
3. Operational Practices
Effective operational practices are crucial for maximizing the production efficiency of a 10 t/h animal feed manufacturing machine.
- Regular Maintenance: Routine maintenance is essential for ensuring that the machine operates at peak efficiency. Regular inspections, lubrication, and replacement of worn components help prevent unexpected breakdowns and maintain consistent production levels.
- Operator Training: Well-trained operators are vital for maximizing production efficiency. Training programs focused on machine operation, troubleshooting, and maintenance empower operators to identify issues early and adhere to best practices for machine care.
- Performance Monitoring: Implementing performance monitoring systems enables feed manufacturers to track key performance indicators (KPIs) such as output rates, energy consumption, and pellet quality. Analyzing this data helps identify trends and areas for improvement, allowing manufacturers to make informed decisions that enhance efficiency.
4. Energy Efficiency
Energy consumption is a significant factor in the overall production costs of feed manufacturing. Improving energy efficiency can lead to substantial cost savings and enhanced profitability.
- Energy-Efficient Motors: Utilizing high-efficiency motors in feed processing machines can reduce energy consumption while maintaining output levels. Investing in energy-efficient technology can result in long-term savings on electricity costs.
- Optimized Process Flow: Streamlining the production process to minimize energy loss is crucial. This includes optimizing the layout of the production line, reducing the distance materials must travel, and ensuring that equipment operates at optimal speeds.
- Heat Recovery Systems: Implementing heat recovery systems can capture excess heat generated during the pelleting process and reuse it for conditioning or other purposes. This not only improves energy efficiency but also lowers overall production costs.
5. Quality Control
Maintaining consistent quality in the final feed product is vital for ensuring customer satisfaction and compliance with industry standards.
- Quality Assurance Protocols: Establishing quality assurance protocols throughout the production process helps identify and address issues that may affect pellet quality. Regular testing of raw materials and finished products ensures that they meet nutritional and safety standards.
- Adjusting Formulations: Based on feedback from quality control, manufacturers may need to modify feed formulations to optimize pellet quality and production efficiency. This adaptability facilitates continuous improvement and responsiveness to market demands.
Conclusion
The production efficiency of a 10 t/h animal feed manufacturing machine is influenced by various factors, including raw material quality, machine design and technology, operational practices, energy efficiency, and quality control measures. By understanding and optimizing these elements, feed manufacturers can enhance their production processes, reduce costs, and improve profitability.
Investing in high-quality machinery, implementing effective maintenance and operational practices, and prioritizing continuous improvement are essential strategies for maximizing animal feed production efficiency. As the demand for high-quality animal feed continues to grow, having a well-installed and efficiently operating feed production line will be crucial for meeting market needs and achieving business objectives.
For details please contact: Richi Machinery
WhatsApp:86 138 3838 9622
Email:enquiry@richipelletmachine.com