As the demand for high-quality animal feed continues to rise, feed manufacturers are increasingly focused on optimizing the efficiency of their production processes. A 25 t/h animal feed production machine is designed to meet the needs of medium to large-scale operations, and enhancing its production efficiency can lead to significant cost savings and improved product quality. This article explores several strategies and best practices that can be employed to maximize the production efficiency of a 25 t/h animal feed production machine.
1. Optimize Raw Material Quality
The quality of raw materials used in the feed production process is one of the most significant factors affecting overall efficiency.
- Supplier Selection: Choose reputable suppliers who provide high-quality raw materials. Conduct regular audits and inspections to ensure that the ingredients meet the required standards.
- Moisture Content: Monitor and control the moisture content of raw materials. Ideal moisture levels (typically between 12-16%) facilitate better conditioning and pelleting, leading to improved pellet quality and reduced energy consumption.
- Particle Size: Ensure that raw materials are ground to the appropriate particle size. Finer particles generally improve mixing and pelleting efficiency, while excessively fine particles can increase friction and energy consumption during processing.
2. Enhance Equipment Efficiency
The efficiency of the machinery itself plays a crucial role in the overall production process. Regular maintenance and timely upgrades can significantly enhance performance.
- Regular Maintenance: Implement a preventive maintenance schedule to ensure that all equipment is functioning optimally. Regularly inspect and service components such as motors, bearings, and belts to prevent unexpected breakdowns.
- Upgrade Components: Consider upgrading critical components, such as pellet mills and mixers, to more efficient models. Advanced technologies, such as ring die pellet mills, can improve output rates and pellet quality.
- Energy Efficiency: Invest in energy-efficient motors and equipment. High-efficiency motors can reduce energy consumption significantly, leading to lower operational costs.
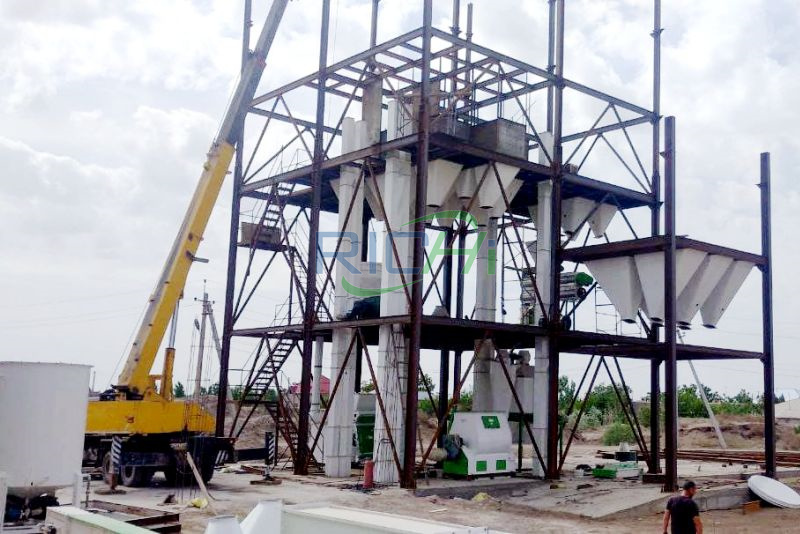
3. Implement Automation and Control Systems
Integrating automation and advanced control systems into the production process can enhance efficiency and consistency.
- Programmable Logic Controllers (PLCs): Use PLCs to automate various processes, such as batching, mixing, and pelleting. PLCs allow for precise control over key parameters, ensuring consistent product quality.
- Human-Machine Interfaces (HMIs): Implement HMIs to provide operators with real-time data on production performance. This enables quick adjustments and helps identify potential issues before they escalate.
- Automated Material Handling: Incorporate automated material handling systems, such as conveyors and bucket elevators, to streamline the movement of raw materials and finished products. This reduces manual labor and minimizes the risk of errors.
4. Optimize Production Processes
Streamlining production processes can lead to significant improvements in efficiency.
- Batching and Mixing: Optimize the batching and mixing processes to ensure uniformity in the feed mixture. Automated batching systems can improve accuracy and reduce the time required for these tasks.
- Conditioning: Proper conditioning of the feed mixture is essential for achieving high-quality pellets. Ensure that the conditioning system is functioning effectively, using steam and moisture control to enhance pellet binding.
- Cooling and Screening: After pelleting, use efficient cooling systems to reduce moisture content and prevent spoilage. Implement screening systems to separate fines and ensure uniform pellet size.
5. Focus on Quality Control
Maintaining consistent quality in the final product is crucial for ensuring customer satisfaction and compliance with industry standards.
- Regular Testing: Establish a routine for testing raw materials and finished products for key quality parameters, such as moisture content, protein levels, and the presence of contaminants. Regular quality checks can identify issues early and allow for timely adjustments.
- Traceability Systems: Implement traceability systems that allow for tracking raw materials from receipt to final product. This ensures that any issues with feed quality can be traced back to their source, facilitating prompt corrective actions.
- Standard Operating Procedures (SOPs): Develop and adhere to SOPs for all aspects of the production process. Clear guidelines ensure that all personnel follow best practices, reducing the risk of errors.
6. Employee Training and Engagement
Well-trained employees are essential for maximizing production efficiency.
- Comprehensive Training Programs: Provide thorough training for operators on the proper operation of the machine, quality control procedures, and best practices for handling raw materials. Training should also cover safety protocols to prevent accidents.
- Encourage Feedback: Foster a culture of open communication where employees can provide feedback on the production process and suggest improvements. Engaging employees in quality assurance efforts can lead to valuable insights and enhancements.
7. Monitor and Analyze Performance
Implementing a system for monitoring and analyzing production performance can help identify areas for improvement.
- Key Performance Indicators (KPIs): Track KPIs such as production output, energy consumption, and feed quality. Analyzing this data can help identify trends and areas for optimization.
- Continuous Improvement: Foster a culture of continuous improvement by regularly reviewing production processes and seeking feedback from operators. This can lead to ongoing efficiency gains over time.
Conclusion
Improving the production efficiency of a 25 t/h animal feed processing machine requires a multifaceted approach that encompasses optimizing raw material quality, enhancing equipment efficiency, implementing automation, optimizing production processes, focusing on quality control, training employees, and monitoring performance.By adopting these strategies, feed manufacturers can maximize output, reduce operational costs, and improve the quality of the feed produced. As the demand for high-quality animal feed continues to grow, investing in these efficiency-enhancing practices will be essential for maintaining a competitive edge in the market.
For details please contact: Richi machinery manufacture
WhatsApp:86 138 3838 9622
Email:enquiry@richipelletmachine.com