As the global demand for animal feed continues to rise, the environmental impact of feed production has become a significant concern. Animal feed mills, particularly those with capacities like 15 t/h, must implement effective environmental protection measures to minimize their ecological footprint while maintaining operational efficiency. This article discusses various strategies and practices that can be adopted to ensure sustainable and environmentally friendly operations in a 15 t/h animal feed mill plant.
1. Raw Material Management
The quality and sourcing of raw materials play a crucial role in minimizing environmental impacts.
- Sustainable Sourcing: Feed mills should prioritize sourcing raw materials from sustainable and responsible suppliers. This includes ensuring that ingredients are produced in an environmentally friendly manner and do not contribute to deforestation or habitat destruction.
- Quality Control: Implementing strict quality control measures for incoming raw materials can help prevent contamination and reduce waste. Regular inspections and testing for contaminants, such as mycotoxins or heavy metals, are essential to ensure that only high-quality materials are used in production.
- Waste Reduction: Efficiently managing raw materials can reduce waste generation. This includes optimizing ingredient usage and minimizing spills during handling and processing.
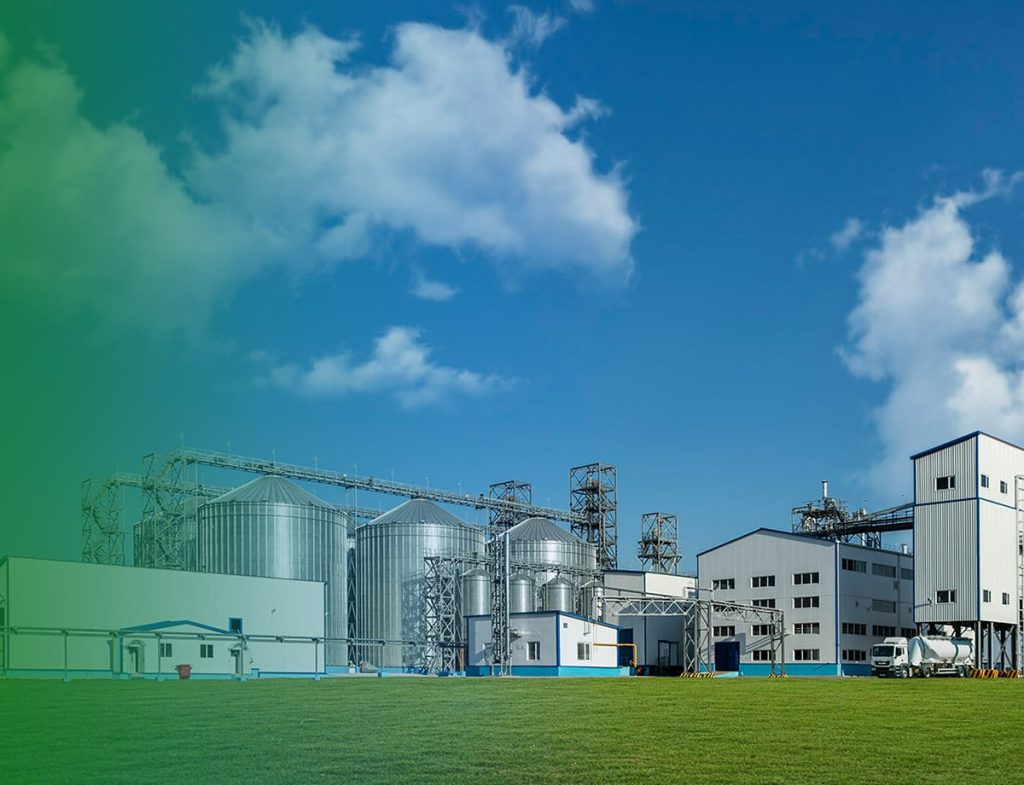
2. Dust Control Measures
Dust generation is a common issue in feed milling operations, which can pose health risks to workers and contribute to air pollution.
- Dust Collection Systems: Installing effective dust collection systems, such as cyclones and baghouses, can capture airborne particles generated during grinding, mixing, and pelleting processes. These systems help maintain air quality within the facility and reduce emissions into the environment.
- Regular Cleaning: Implementing a routine cleaning schedule to remove dust and debris from equipment and work areas is essential. This not only improves air quality but also enhances safety by reducing slip hazards.
- Negative Pressure Ventilation: Utilizing negative pressure ventilation systems can help control dust by creating a vacuum effect that draws dust away from work areas and into collection systems.
3. Waste Management Practices
Proper waste management is critical for minimizing the environmental impact of a feed mill factory.
- Solid Waste Management: Establishing a comprehensive waste management plan that includes the proper disposal of solid waste generated during production is essential. This can involve recycling by-products, such as fines and dust, back into the production process or utilizing them for other applications, such as animal bedding.
- Liquid Waste Management: If the feed mill generates liquid waste, it is important to implement systems for treating and managing this waste to prevent contamination of local water sources. This may involve using settling tanks or biological treatment systems to process wastewater before discharge.
- Composting: Implementing composting programs for organic waste, such as expired feed or rejected pellets, can help divert waste from landfills and create valuable soil amendments for local agriculture.
4. Energy Efficiency Measures
Improving energy efficiency not only reduces operational costs but also minimizes the environmental impact of feed production.
- Energy-Efficient Equipment: Investing in energy-efficient machinery, such as high-efficiency motors and variable frequency drives (VFDs), can significantly reduce energy consumption during production. This leads to lower greenhouse gas emissions and operational costs.
- Heat Recovery Systems: Implementing heat recovery systems can capture excess heat generated during the pelleting process and reuse it for conditioning or other purposes. This enhances overall energy efficiency and reduces the need for additional energy sources.
- Renewable Energy Sources: Where feasible, integrating renewable energy sources, such as solar panels or wind turbines, can help power the feed mill and reduce reliance on fossil fuels.
5. Emission Control
Controlling emissions is essential for minimizing the environmental impact of feed production.
- Air Quality Monitoring: Regularly monitoring air quality within and around the feed mill can help identify potential sources of pollution and ensure compliance with local regulations. This may involve using air quality sensors to track particulate matter and volatile organic compounds (VOCs).
- Emission Control Technologies: Implementing technologies such as scrubbers and filters can help reduce emissions from the feed milling process. These systems can capture and neutralize harmful pollutants before they are released into the atmosphere.
6. Employee Training and Engagement
Engaging employees in environmental protection efforts is crucial for fostering a culture of sustainability within the feed mill.
- Training Programs: Providing training on environmental best practices and the importance of sustainability can empower employees to contribute to reducing the facility’s environmental footprint. Topics may include waste management, energy conservation, and pollution prevention.
- Encouraging Innovation: Creating a culture of innovation and encouraging employees to suggest improvements can lead to new ideas for enhancing sustainability in operations. Recognizing and rewarding employees for their contributions can further motivate engagement.
7. Compliance with Regulations
Adhering to environmental regulations and standards is essential for ensuring that the feed mill operates sustainably.
- Environmental Impact Assessments (EIAs): Conducting thorough EIAs before starting new projects or expansions can help identify potential environmental impacts and develop strategies to mitigate them. Engaging with local regulatory agencies can ensure compliance with environmental laws.
- Sustainability Certifications: Pursuing sustainability certifications, such as ISO 14001 (Environmental Management Systems), can demonstrate a commitment to environmental stewardship and continuous improvement in environmental performance.
Conclusion
Implementing effective environmental protection measures in a 15 t/h animal feed mill plant is essential for minimizing its ecological footprint while maintaining operational efficiency. By focusing on sustainable raw material management, dust control, waste management, energy efficiency, emission control, employee engagement, and regulatory compliance, feed manufacturers can contribute to a more sustainable future.As the demand for high-quality animal feed continues to grow, prioritizing environmental responsibility will not only enhance the reputation of feed producers but also ensure long-term success in the competitive animal feed market. Investing in these measures is not just beneficial for the environment; it is also a strategic move that can lead to improved operational efficiency and profitability.
For details please contact: Richi manufacture
WhatsApp:86 138 3838 9622
Email:enquiry@richipelletmachine.com